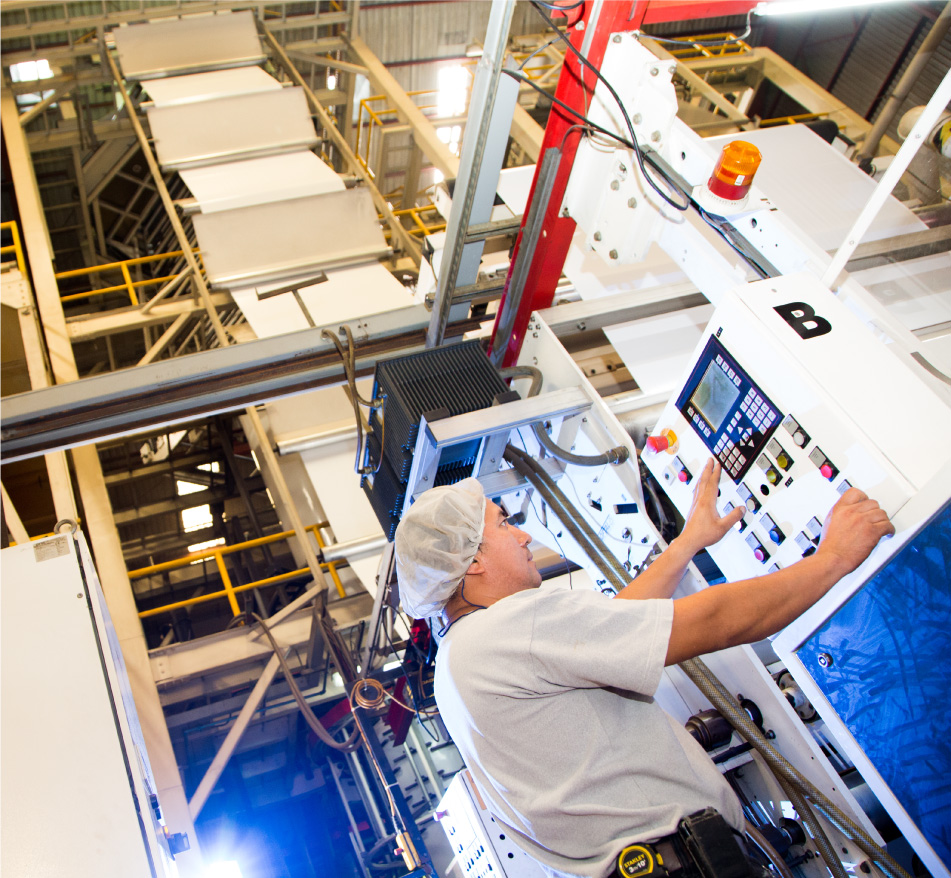
Procesos
Extrusión de Película
Uno de los métodos más comunes en la elaboración de empaque flexible es el de Extrusión de Película Soplada. El proceso considera la extrusión de plástico a través de un molde circular para formar un tubo delgado el cual mediante la inyección de aire toma la forma de una burbuja. Un anillo de enfriamiento que se encuentra sobre el molde sopla aire a alta velocidad sobre la burbuja con el objetivo de enfriarla.
El tubo sigue su recorrido hacia arriba disipando calor hasta llegar a los rodillos de tiro, en donde el tubo pasa a ser lo que se conoce como tubo plano. Este tubo desciende por los rodillos de bajada.
Finalmente, la película plana es conservada como tubo o bien los extremos son retirados para dar paso a dos lienzos. Esta película es enrollada posteriormente sobre centros de cartón.
Las aplicaciones típicas incluyen película para Empaque industrial, Empaque para el consumidor, Película para laminación, Película de barrera, Película para la Agricultura, entre muchas otras.
Proceso de Impresión
Impresión: Durante esta etapa el rodillo anilox pasa por la cámara que está compuesta por una bandeja y una racla, en donde la bandeja es la que recibe la tinta preparada y la racla es la que quita el excedente de tinta que pueda tener el anilox. En este punto se debe de controlar la cantidad de tinta que posee la bandeja debido a que si es baja la tinta se secará rápido y provocará impresiones deficientes. Luego el anilox es el encargado de transferir la tinta hacia el sello (Clisé) y este hacía la película (sustrato).
Secado de material impreso: Después de que la tinta ya se encuentra en el sustrato se procede al secado de cada una de las tintas transferidas al sustrato, al no hacerlo se puede originar una fusión de los colores que se superponen dando impresiones deficientes, esta parte de la impresora se conoce como tinteros. Las temperaturas adecuadas en este proceso van de los 50-90 grados centígrados
Extracción de solvente: Esta etapa también es una etapa de secado en donde una mala extracción puede originar solventes retenidos, factores de vital importancia a controlar durante esta etapa son las temperaturas, tiempo de estadía en el túnel del sustrato y el caudal del aire circulante. En este punto tratar el tiempo de estadía del sustrato en el túnel de secado resulta en bajar velocidad, por lo que es una práctica no económica. En base a esto se controlan las temperaturas que van desde los 50-90 grados centígrados, temperaturas bajo las cuales no se han presentado solventes retenidos.
Enfriado de material impreso: Para esta etapa del proceso se utiliza un rodillo por el cual circula agua fría, esto con el propósito de que la calandria actúe como un intercambiador de calor debido a la transferencia de calor que realiza entre dos medios, el sustrato y la baja temperatura del fluido. Esta operación le da una estabilización al material para evitar que no se deforme o se pegue.
Embobinado: En esta etapa se enrolla la película en el centro de cartón establecido durante la colocación de cores.
Proceso de Laminación
Los sistemas de laminación pueden ser clasificados de acuerdo con los materiales y el adhesivo que va a ser utilizado. Dentro de los sistemas más utilizados, y en los que nos enfocaremos en este post, figuran: La laminación base solvente y la laminación sin solventes.
Estas dos clasificaciones rigen las configuraciones de las máquinas laminadoras utilizadas en cada uno de dichos procesos.
Tipos de laminación y máquinas laminadoras
Una laminadora tradicionalmente está compuesta por las siguientes partes:
- Desembobinador primario y secundario de los materiales que van a ser laminados. En el caso de una laminadora dúplex (procesa bilaminados en un paso).
- Unidad de aplicación de adhesivos
- Horno de secado en el caso de laminación con solventes
- Rodillos de transferencia
- Unidad laminadora
- Embobinador
- Alineadores de banda
Proceso de Slitter
El proceso de Slitter consiste en cortar longitudinalmente los materiales a base de polimeros que viene de un ancho mayor y se obtiene como producto final el corte de una o varias cintas de menor ancho y peso conforme las especificaciones del cliente. Los factores que se deben de considerar son: tipo de material, ancho del material, calibre del material, el peso de las bobinas a cortar, el peso de las bobinas de producto terminado, así como el volumen total a producir por lote, todo tiene influencia en la configuración de la linea y las necesidades requeridas para entregar al cliente bobinas de mayor calidad.
Las variables del control del proceso para garantizar la calidad del producto son: Tensiones iniciales y finales, tipo de embobinado, tolerancia en pesaje, mediciones de COF y fuerzas Bond, gramaje, distancias entre fotoceldas, calidad en el diseño del arte.
En el área de corte de Slitter se tiene un compromiso mayor hacia a la Inocuidad del producto, manteniendo los estandares de operación y controles exahustivos en los insumos que puedan generar una contaminación hacia el producto final.
Proceso de Corte
Nuestras bolsas son producidas por medio de sello caliente y corte de rollos con o sin impresión, así como laminadas siguiendo uno de dos métodos básicos; sello lateral o sello fondo.
Los rollos pueden presentase en la forma de tubo, tubo con fuelles o lienzo.
La película es alimentada a una máquina la cual de acuerdo a la longitud requerida por nuestros clientes realiza un ciclo de colocación de sello y corte para crear bolsas individuales. Manijas pueden ser recortadas o colocadas bajo especificaciones del cliente para ciertos productos.
Este proceso tiene la habilidad de aportar miles de bolsas por minuto manteniendo siempre en mente un alto estándar de Calidad y productividad en nuestros muy diversos tipos de producto.